Alternatives to Stick-Built Construction: Prefab Homebuilding Methods and Materials
- Encompass CRM
- Dec 15, 2020
- 4 min read
Updated: Jan 13, 2021
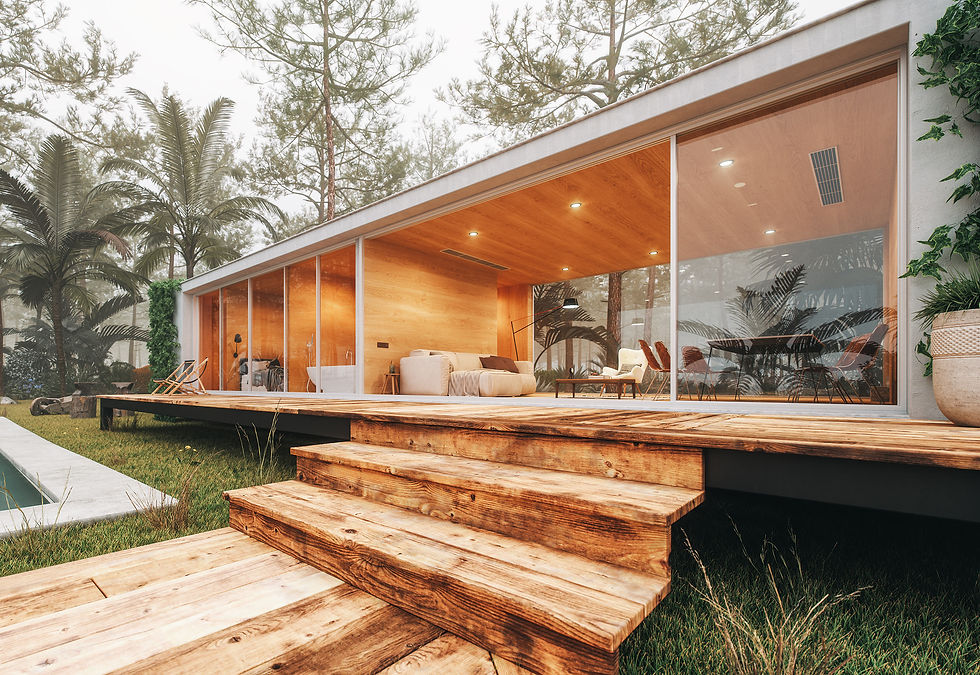
Shorter construction times, lower costs, and sustainability concerns are motivating homebuyers to look for new ways to build their homes. Prefabricated (prefab) homes, usually constructed from mass-produced sections or “modules,” are gaining ground as the supply of affordable and eco-friendly housing has dwindled. If you’re considering a new-home build, these alternatives to traditional homebuilding might be just the solution you’re looking for.
Prefabrication cuts down on mistakes and waste, speeds up production time since factory construction and land prep can occur simultaneously, often uses sustainable and recyclable materials, and provides improved energy efficiency for your new home.
Shipping Containers
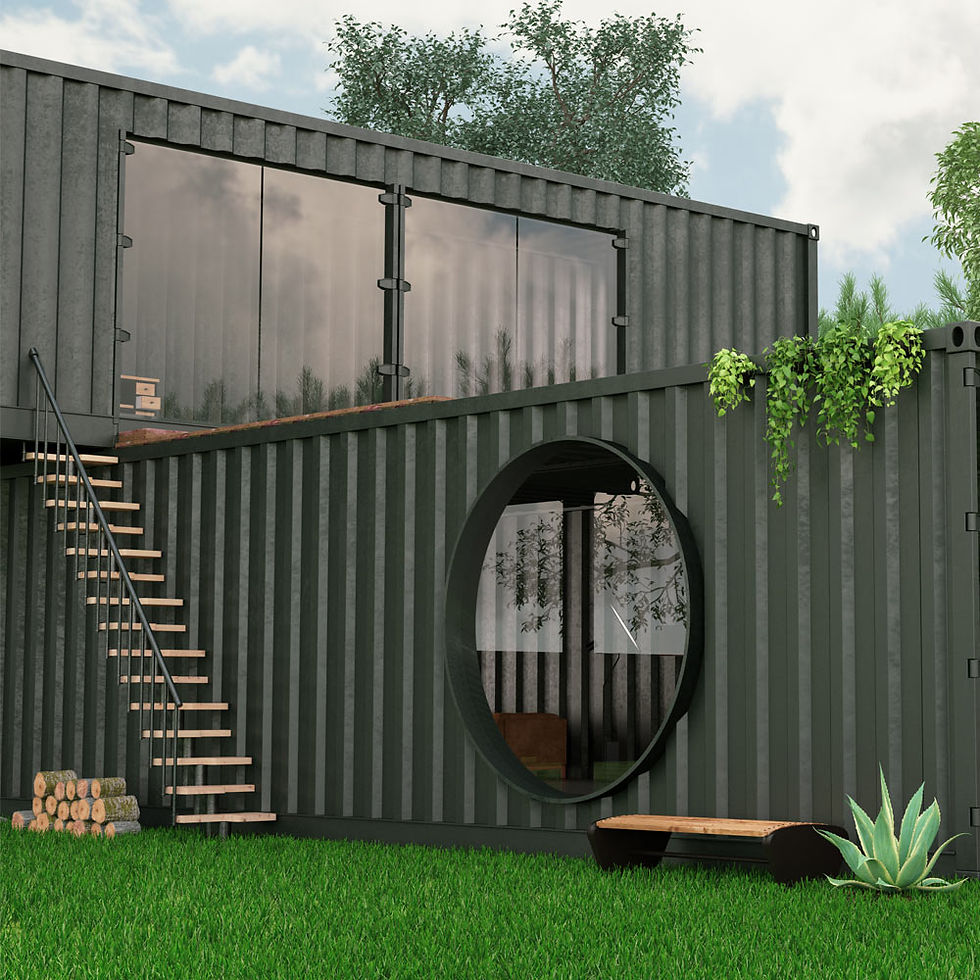
What it is: Huge metal boxes are used to carry products aboard large ships. Once used, they’ve become trendy in some areas as a lower-cost way to create housing (and other buildings).
Pros: Kits are available, or you can work with an architect to design your home. Skilled DIYers may be able to do much of the work themselves, saving time and money. Containers can be stacked in different ways to customize your home’s layout.
Old shipping containers:
Keep your costs down
Recycle big hunks of metal
Can be easier to locate and purchase
New shipping containers:
Let you choose the size, and with some companies, some pre-installed features
Last for decades
Never carried any toxic materials
Aren’t treated with chemicals
Cons: You’ll need to review local zoning laws and obtain special permits for shipping-container housing. Because they are made of steel, the thin walls can be difficult to insulate. Plus, it could be more challenging to get a mortgage for this type of home, and resale could also be more difficult.[1]
Old shipping containers:
Can be rusted or damaged
May contain toxic residue from previous use
May have been treated with chemicals
New shipping containers:
Aren’t eco-friendly: they require new materials to be sourced
Can be double the cost of old containers
Often take a very long time to arrive
Modular Construction[2]

What it is: Modular home parts are constructed in a factory, using materials and construction standards you’d find in a typical home, then shipped to the home location and put together on site.
Pros: Built to conform to your local building codes, they often include fixtures, flooring, and electrical and plumbing components. Homes can be taken apart and reconfigured, or the individual parts can be reused elsewhere. A few companies sell DIY kits for modular homes. A high level of skill is not needed to put them together.
Cons: Many parts for modular homes are built outside the U.S. and then shipped in for use. Each section can only be as large as the truck transporting it. You may require two different types of loans — but don’t worry; we can help you navigate your financing options.
Structural Insulated Panels (SIPs)

What it is: Panelized homes are made from sheets of insulation sandwiched between the panel’s inner and outer layers. Channels for electrical wires are preset into the walls. Insulation varies in materials and thickness.
According to a survey by Dodge Data and Analytics and the Modular Building Institute, SIPs have been an important component of homebuilding recently.
% of Projects Using SIPs in the Past Three Years

Source: Dodge Data & Analytics, 2020
Pros: Can reduce construction time by 50% and labor time by 30% compared to stick-built homes.[3] Increases heat resistance and decreases air loss. Generally eco-friendly, made from trees that are fast-growing but less commonly used in traditional on-site building. Using SIPs can significantly reduce energy costs over the long term because of their excellent insulation.[3]
Cons: Because they are airtight, SIP buildings require fans or blowers to circulate air throughout the home. Panels must be joined with a compound made especially for SIPs. Panel materials may attract insects such as termites and carpenter ants, though there are methods available to deter them.[3] Uses petroleum-based products in construction. Difficult to remodel.
Insulating Concrete Forms (ICFs)

What it is: Sheets of insulating foam are manufactured off-site and transported to the building site, where they are erected. Concrete is then poured between the foam to form the core of the walls.
Pros: Mold-, moisture-, and fire-resistant.[4] Many design options are available. ICFs are double insulated, which also makes them quieter. Walls are reinforced with steel, helping them stand up to severe weather and earthquakes.
Cons: Higher cost of materials. Prone to condensation, necessitating installation of a dehumidifier. Difficult to waterproof. Needs a builder experienced in this type of construction. Prone to termites, which like tunneling through the foam. Difficult to remodel.[5]
Prefab Corrugated Steel

What it is: Sheets of steel galvanized to withstand the weather and bent into a pattern of waves to give it strength for use in construction.
Pros: Recyclable, durable, and low-maintenance. Expect corrugated metal to last between 40 and 70 years. Reduces on-site construction waste.[6] Build kits are available. Can be made in almost any home style you choose.
Cons: Because metal expands and contracts with changes in the weather, it’s critical to factor in some “breathing room” when attaching fasteners. Metal can be noisy and difficult to match in color if replacement panels are needed.
Comments